How to Troubleshoot Common Issues with Automatic Carton Machines?
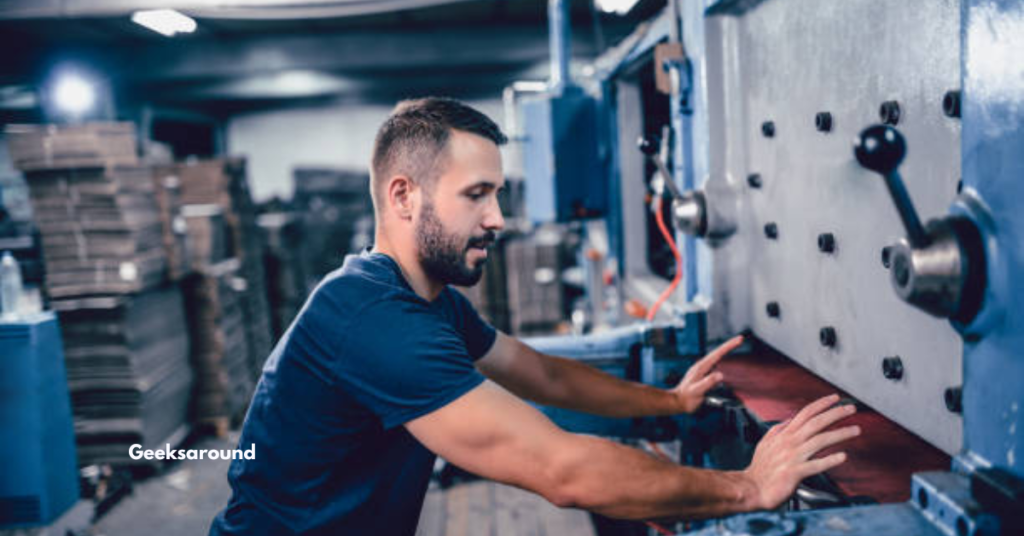
Automatic carton machines are essential in many industries for packaging products efficiently and consistently. However, like all machinery, they can occasionally encounter issues that disrupt operations and cause delays. Troubleshooting these issues promptly and effectively is crucial to maintaining productivity and ensuring smooth operation.
This guide post will provide a comprehensive guide on how to troubleshoot common issues with automatic carton machines. By understanding these troubleshooting techniques, you can minimize downtime and keep your packaging processes running smoothly.
1. Machine Won’t Start
One of the most common issues with automatic carton machine is when they fail to start. This can be due to various reasons, including electrical problems, mechanical faults, or user errors. To troubleshoot this issue:
- Check the Power Supply: Ensure that the machine is properly plugged in and that there is power at the outlet. Verify that all switches and circuit breakers are in the correct position.
- Inspect Fuses and Circuit Breakers: A blown fuse or tripped circuit breaker can prevent the machine from starting. Replace any blown fuses and reset any tripped breakers.
- Examine Safety Interlocks: Many automatic carton machines have safety interlocks that prevent the machine from operating if certain conditions are not met. Check that all guards and doors are securely closed and that all safety sensors are functioning correctly.
- Review the User Manual: Refer to the machine’s user manual for specific troubleshooting steps and ensure that all startup procedures are followed correctly.
2. Carton Jams
Carton jams are another common issue that can halt production. Jams can occur for several reasons, including misaligned cartons, incorrect carton sizes, or mechanical faults. To troubleshoot carton jams:
- Clear the Jam: Carefully remove any jammed cartons from the machine, following the manufacturer’s instructions to avoid damage or injury.
- Check Carton Alignment: Ensure that cartons are properly aligned and fed into the machine correctly. Misaligned cartons can cause jams and disrupt the packaging process.
- Verify Carton Size and Quality: Make sure that the cartons being used are the correct size and quality for the machine. Using cartons that are too large, too small, or of poor quality can lead to jams.
- Inspect the Feed Mechanism: Check the feed mechanism for any obstructions or mechanical issues that could be causing jams. Clean and lubricate the mechanism as needed to ensure smooth operation.
3. Poor Carton Sealing
Inadequate or inconsistent carton sealing can result in damaged products and customer dissatisfaction. To troubleshoot poor carton sealing:
- Check Sealing Mechanisms: Inspect the sealing mechanisms, such as gluing or taping units, to ensure they are functioning correctly. Look for any obstructions, wear, or damage that could be affecting the sealing process.
- Adjust Sealing Settings: Verify that the sealing settings are correctly adjusted for the type of cartons being used. Adjust the temperature, pressure, or adhesive application as needed to achieve consistent sealing.
- Use High-Quality Adhesives: Ensure that the adhesives being used are of high quality and suitable for the cartons. Low-quality or incompatible adhesives can result in poor sealing.
- Regular Maintenance: Perform regular maintenance on the sealing mechanisms to keep them in good working condition. This includes cleaning, lubricating, and replacing worn parts as needed.
For more detailed information and expert solutions, visit ELITER.
4. Inconsistent Carton Forming
Inconsistent carton forming can lead to improperly shaped cartons that do not protect the contents adequately. To troubleshoot inconsistent carton forming:
- Inspect Forming Tools: Check the forming tools for wear, damage, or misalignment. Replace or repair any faulty tools to ensure consistent carton forming.
- Adjust Forming Settings: Verify that the forming settings are correctly adjusted for the type of cartons being used. Adjust the pressure, speed, or other settings as needed to achieve consistent forming.
- Monitor Carton Quality: Ensure that the cartons being used are of consistent quality and meet the machine’s specifications. Variations in carton quality can lead to inconsistent forming.
- Regular Maintenance: Perform regular maintenance on the forming tools and mechanisms to keep them in good working condition. This includes cleaning, lubricating, and replacing worn parts as needed.
5. Machine Stops Mid-Cycle
If your automatic carton machine stops mid-cycle, it can be due to a variety of issues, including electrical faults, mechanical problems, or safety interlocks. To troubleshoot this issue:
- Check for Error Messages: Many automatic carton machines have error message displays that provide information about the issue. Refer to the user manual to interpret these messages and take appropriate action.
- Inspect Electrical Connections: Ensure that all electrical connections are secure and free from damage. Loose or damaged connections can cause the machine to stop unexpectedly.
- Examine Safety Sensors: Check that all safety sensors are functioning correctly and that there are no obstructions or misalignments. Faulty or triggered sensors can cause the machine to stop mid-cycle.
- Review Maintenance Logs: Refer to the machine’s maintenance logs to identify any recent issues or maintenance activities that could be related to the problem. Address any outstanding maintenance needs promptly.
6. Inconsistent Product Placement
Inconsistent product placement within the cartons can lead to damaged goods and poor presentation. To troubleshoot inconsistent product placement:
- Check Product Feed System: Inspect the product feed system for any obstructions, misalignments, or mechanical issues. Ensure that products are being fed into the machine consistently and correctly.
- Adjust Placement Settings: Verify that the placement settings are correctly adjusted for the type of products being packaged. Adjust the speed, position, or other settings as needed to achieve consistent placement.
- Monitor Product Quality: Ensure that the products being packaged are of consistent quality and meet the machine’s specifications. Variations in product quality can lead to inconsistent placement.
- Regular Maintenance: Perform regular maintenance on the product feed system and placement mechanisms to keep them in good working condition. This includes cleaning, lubricating, and replacing worn parts as needed.
7. Excessive Noise and Vibration
Excessive noise and vibration can indicate underlying issues with the machine that need to be addressed promptly. To troubleshoot excessive noise and vibration:
- Inspect Moving Parts: Check all moving parts for wear, damage, or misalignment. Replace or repair any faulty parts to reduce noise and vibration.
- Tighten Loose Components: Ensure that all components are securely fastened. Loose components can cause excessive noise and vibration.
- Lubricate Moving Parts: Regularly lubricate all moving parts to reduce friction and wear, which can cause noise and vibration.
- Balance the Machine: Ensure that the machine is properly balanced and level. An unbalanced machine can cause excessive noise and vibration.
8. Frequent Downtime
Frequent downtime can significantly impact productivity and profitability. To troubleshoot frequent downtime:
- Review Maintenance Schedule: Ensure that regular maintenance is being performed according to the manufacturer’s recommendations. Address any outstanding maintenance needs promptly.
- Analyze Downtime Causes: Track and analyze the causes of downtime to identify recurring issues. Implement corrective actions to address these issues and reduce downtime.
- Train Operators: Ensure that all operators are properly trained on the machine’s operation, maintenance, and troubleshooting procedures. Well-trained operators can help prevent issues and minimize downtime.
- Upgrade Machinery: If the machine is outdated or no longer meets your production needs, consider upgrading to a newer, more reliable model.
FAQs
What should I do if my automatic carton machine won’t start?
First, check the power supply, fuses, circuit breakers, and safety interlocks. Ensure that all startup procedures are followed correctly as outlined in the user manual. If the issue persists, contact the manufacturer for further assistance.
How can I prevent carton jams in my automatic carton machine?
To prevent carton jams, ensure proper carton alignment, use the correct carton size and quality, and regularly inspect and maintain the feed mechanism. Clear any jams promptly and follow the manufacturer’s guidelines for operation and maintenance.
What causes poor carton sealing, and how can I fix it?
Poor carton sealing can be caused by faulty sealing mechanisms, incorrect settings, or low-quality adhesives. Inspect the sealing mechanisms, adjust the settings as needed, and use high-quality adhesives. Regular maintenance is also crucial to ensure proper sealing.
How can I reduce excessive noise and vibration in my automatic carton machine?
To reduce noise and vibration, inspect moving parts for wear or damage, tighten loose components, lubricate moving parts regularly, and ensure the machine is properly balanced and level. Address any underlying mechanical issues promptly.
Conclusion
Troubleshooting common issues with automatic carton machines is essential for maintaining productivity and ensuring smooth operation. By addressing problems such as machine startup failures, carton jams, poor sealing, inconsistent forming, mid-cycle stops, inconsistent product placement, excessive noise, and frequent downtime, you can minimize disruptions and keep your packaging processes running efficiently. Regular maintenance, proper operator training, and timely upgrades are key to preventing issues and maximizing the performance of your automatic carton machine.